Introduction of Beamo for the Digitalization of Training Programs in a Major Airline
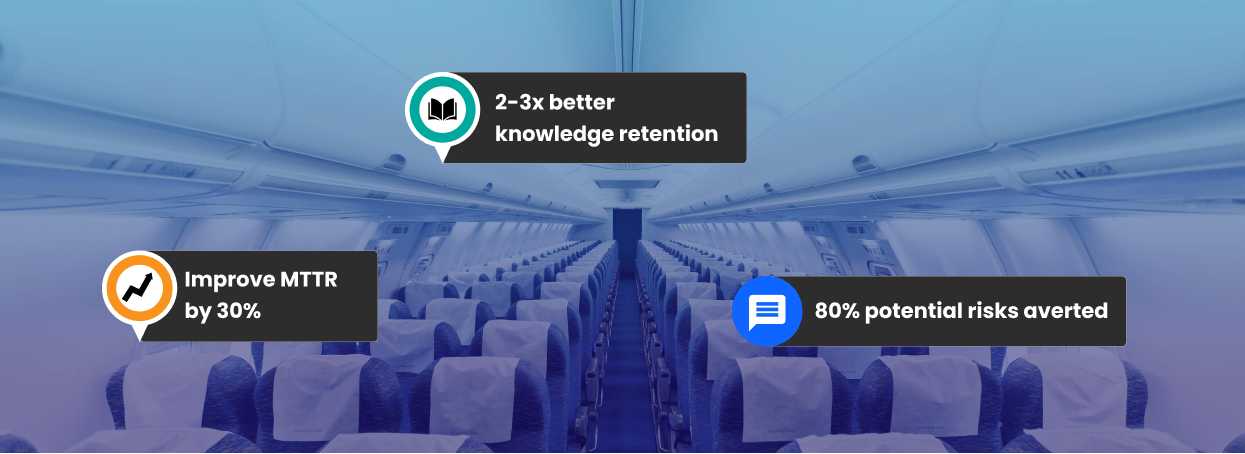
- Experiencing various aircraft types virtually and conducting crew training within the digital twin.
- Providing updates on cabin operations within the digital twin by attaching notices.
- Enabling detailed report generation by uploading photos of issues inside the cabin to the digital twin.
- Performing aircraft cabin inspection using the digital twin for cost savings in maintenance.
A major airline operates more than 100 aircraft continuously. Each type of aircraft is equipped with various configurations of cabin seats and equipment.
The airline aimed to efficiently conduct crew training for various types of aircraft using digital twins. The company sought to improve its workflow not only for remote training but also for report generation and aircraft cabin inspections by leveraging digital twins.
Challenges in learning various types of aircraft
The client sought the adoption of digital twins as an effective method for employee training. The company faced challenges in educating and training crews working on numerous aircraft operated by the airline. Even after training, employees struggled to adapt due to the deployment of various aircraft types and equipment, making it difficult to grasp the nuances, despite the presence of aircraft operation manuals within the cabins.
Additionally, upon the aircraft's arrival at destination airports, cleaning procedures took place. During such instances, if immediate actions were required, the crew would create written reports detailing equipment malfunctions, damage conditions, or other issues, forwarding them to maintenance personnel at headquarters or hubs. However, these written reports sometimes lacked context or sufficient details, leading to inadequate follow-up actions.
Improving workflow based on spatial information
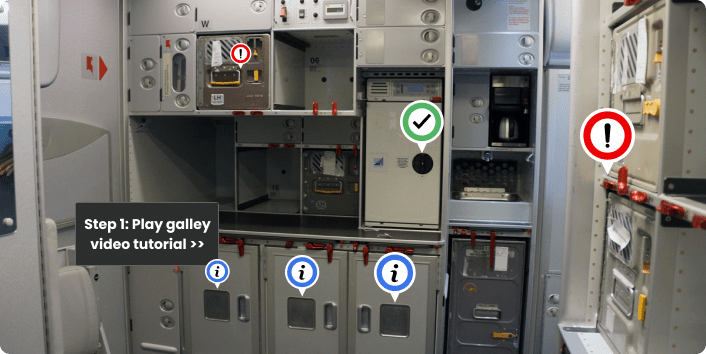
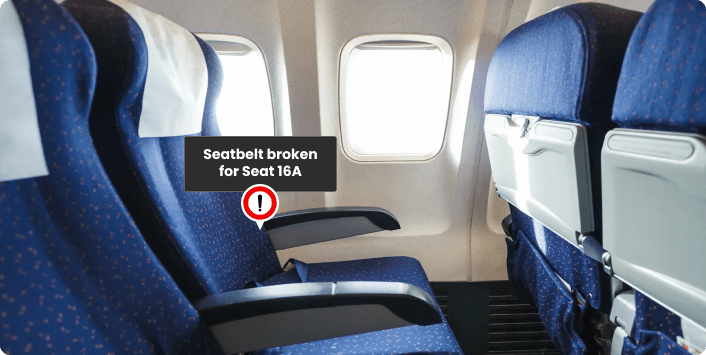
Beamo helped to improve education and training for flight attendants.
The airline introduced Beamo to digitize its training programs and minimize errors in post-flight reporting by leveraging spatial information. Utilizing 360 cameras, smartphones, and the Beamo Starter Kit, they captured the interior of aircraft and created a digital twin. This enabled spatial-information-based employee training.
Due to the varying manuals for different aircraft types, the digital twin incorporated a tagging feature, allowing the upload of short training videos, operation manuals, and procedural documents. This ensured that the crew could access this information at any time. When operating procedures were updated or equipment changed, the airline's training department uploaded the latest documents and videos to the digital platform, allowing remote access for the crew.
Beamo helped to minimize reporting errors on landing.
The digital twin also replaced traditional written reports during landing. Crew members could use their phones or tablets to tag issues within the digital twin, generate reports, and notify ground personnel. Crew members could upload photos for detailed reporting, and maintenance personnel found it easier to assess the severity of issues and prepare for necessary tasks through the uploaded images.
Optimizing aircraft operations
through digital twin utilization
The adoption of digital twins has enabled the client to establish a system for employee training and reporting based on spatial information. Crew members can now virtually experience various types of aircraft, receiving necessary training remotely. Post-training, they can stay updated on changes in aircraft cabin operations and engage in self-training.
Additionally, the airline has utilized Beamo for aircraft cabin inspections, leading to cost savings in maintenance, minimizing errors, and achieving a 30% improvement in Mean Time To Repair (MTTR). Leveraging spatial information for issue identification has not only optimized workforce deployment for necessary actions but also resulted in a 30% reduction in transportation costs.
The airline is now exploring the creation of digital twins for warehouses and logistics centers to facilitate remote inspections, information sharing, and long-distance collaboration. Furthermore, they plan to use Beamo for visual inspections, not only for interior checks but also for exterior maintenance tasks on aircraft.