A Case Study of a Global Manufacturer Utilizing Beamo
for Immersive Information Management
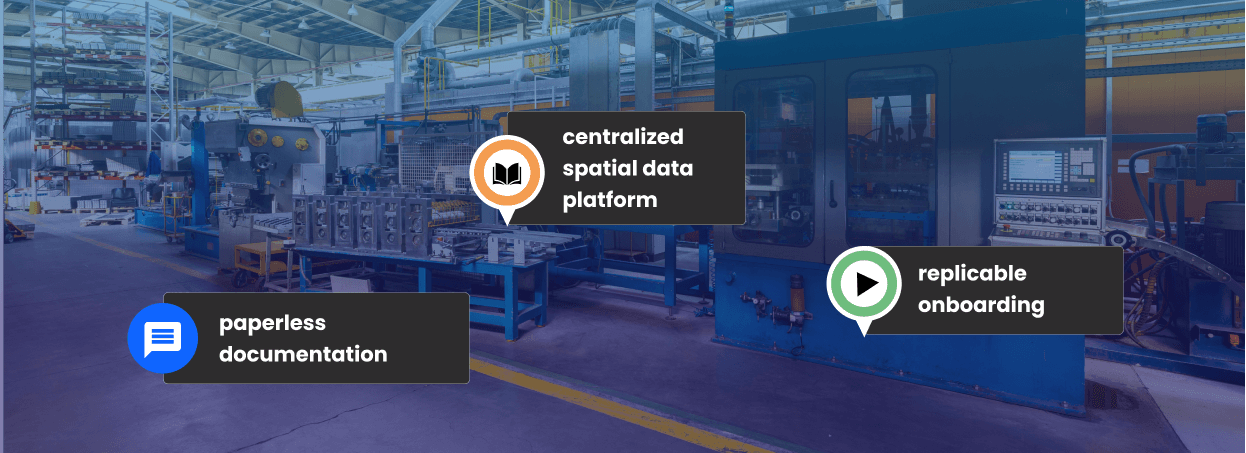
- Prevention of production process disruptions and assembly line freezes
- Elimination of paper-based documentation
- Reduction of unnecessary on-site movements
- Enhanced collaboration through highly customized strategies for group management
- Improved continuity in maintenance records and shift work
- User access permissions and information segmentation based on tasks, reinforcing security
- Enhanced organizational adaptation for new employees
The global manufacturer introduced in this case study is a specialized company producing electronic components such as lithium-ion batteries, semiconductors, image sensors, camera modules, and displays for various global clients.
Capture and digitize the challenging environment inside the factory with low light conditions and high vibrations, and achieve immersive information management and enhance workflow continuity by integrating existing factory data into the established digital twin.
Preventing work record omissions
affecting work continuity
The client sought to prevent the omission of work records that could occur during shift changes and aimed to introduce a digital twin for efficient documentation. While equipment on the production line continued to operate, the maintenance team worked in shifts. Therefore, recording work details was crucial for workflow continuity. Previously, paper records for work were placed in front of each piece of equipment, and Excel documents and work reports were uploaded to the EDM to share information with other teams.
Additionally, the client was looking for more efficient methods to educate new employees, who often had to be repeatedly guided on accessing specific locations within the workplace and the locations of various equipment.
The client, considering the enhancement of workflow continuity and strengthening communication among team members and departments by adding spatial information to existing factory data, contemplated the introduction of a digital twin. In addition to this, they aimed to use the Beamo solution for purposes such as safety training and onboarding education for employees, pre-visit preparations for site inspections, and collaborative facility management.
Enhancing work continuity based on
spatial information
%20copy.png)
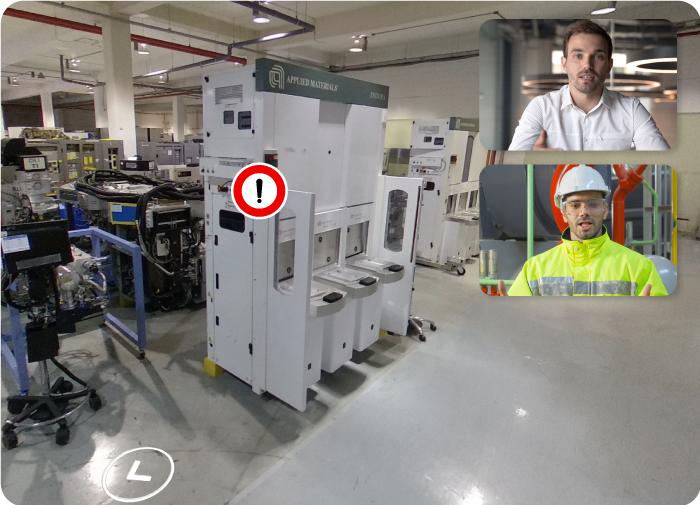
After the introduction of Beamo, the client can now store work records, previously written on paper, within the digital twin. Using a 360 camera and the Beamo app, they capture the on-site environment, generating a digital twin used as a centralized platform.
Within the virtual 3D facility space, the tagging feature allows recording work details and attaching documents, promoting documentation and collaboration. This strengthens workflow continuity, especially in the context of shift work.
The client utilizes the digital twin for training new employees, enabling immersive education about facilities and equipment without the need to navigate the entire facility physically.
Moreover, the virtual 3D space is leveraged for regular safety training, pre-visit preparations for on-site inspections, facility management, and equipment history checks.
Minimizing downtime and
strengthening collaboration
The client has implemented Beamo to establish a new system for organizing existing factory data spatially, preventing downtime and enhancing collaboration. The client, with an average area of 18,000 square meters and more than 12 manufacturing facilities, utilizes Beamo on its corporate campus. Paper-based memos for work records have been replaced with tags in Beamo's 3D workspace, allowing anyone to access work records anytime, anywhere.
Thanks to Beamo's digital twin, which seamlessly integrates with other software, the client can retrieve and review various necessary documents such as maintenance information, operating manuals, and CAD files within a single platform. This significantly contributes to optimizing the continuity of production operations.
As a result, the team can effectively manage diverse factory data based on immersive spatial information, enhancing communication and collaboration. The digital twin built with Beamo can serve as infrastructure for implementing futuristic AR and Internet of Things (IoT) applications.